Solar Module Test Project
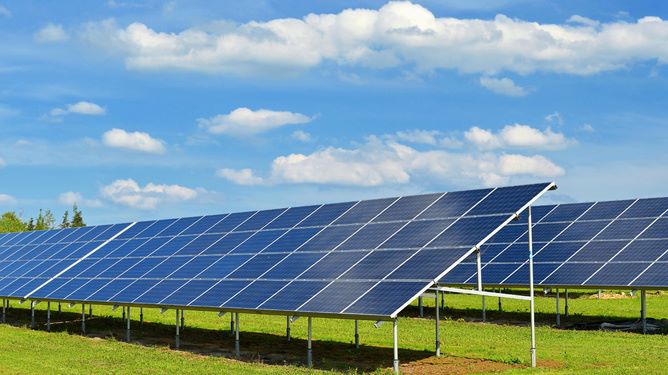
1. solar module reliability test specification:
The reliability test of the solar module is to confirm the performance of the solar module (early), and the test specifications for the module are mainly IEC61215, IEC61646, UL1703 three test specifications. IEC61215 is suitable for crystalline (Si) modules; IEC61646 is suitable for thin-film (Thin-flm) modules; The UL1703 is suitable for both crystalline and thin film solar modules. In addition, the GB and CNS solar energy specifications are partially modified from the IEC.
2. the relationship and importance of Macro Exhibition and solar energy test projects:
According to IEC61215, IEC61646 test items a total of about 10 (solar module test items corresponding to the general table). Among them, the test equipment manufactured by Hongjian will be used, and the relevant test conditions are temperature cycling (Thermal cycling, 10.11). There are three categories of Humidity freeze (10.12) and Damp heat (10.13), while UL1703 only has two items of temperature cycle wet freezing without the item of damp heat.
3. Thermal cycling test (Thermal cycling)lEC61215-10-11:
Solar module temperature cycle test is used to determine the fatigue, thermal failure, or other stress failure caused by repeated changes in temperature of the module. The current number of temperature cycles is 200 times, and the future trend will be 600 times (according to the test results of the American Association for Renewable Energy [NREL], the power degradation rate of 600 times is greater than 200 times as much as twice).
Through the temperature cycle: defects of the module can be found: crack growth, module cracks, warping, sealing material delamination, point shedding, glass corrosion... Let's wait.
Temperature conditions: Low temperature :-40℃, high temperature :85°C(IEC), 90 °C(UL), the fastest temperature variability (average):100 °C /h, 120 °C /h, relevant measurements need to be carried out during the test (using the Qingsheng solar energy measurement system), the test process needs to measure the module: module surface temperature, voltage and current, ground continuity, insulation... Let's wait.
4. the purpose of the temperature cycle test process through bias:
Temperature cycle test process, the specification requires through bias, the purpose of the test is to make the defective Cell heat to accelerate aging and accelerate failure test purposes, so it needs to be energized above 25℃ during the temperature cycle process, the laboratory in the United States has statistics, It was found that the difference between the failure rate of the solar module with power and without power is as high as 30%, and the experimental data indicates that if there is no power, the solar module is not easy to fail in the temperature cycle environment, so when carrying out the temperature cycle test of the solar cell (Cel)& module, it needs to be matched with a special measurement system.
5. the introduction of wet freezing test lEC61215-10-12:
Description: To determine whether the component is sufficiently resistant to corrosion damage and the ability of moisture expansion to expand the material molecules, frozen moisture is the stress to determine the cause of failure. For the product to be tested, the test stress is high temperature and high humidity (85℃/85%R.H) to low temperature (-40℃ humidity 85%R.H). Maintain to 25℃), and low temperature rise to high temperature and high humidity, rather than 85℃/85%R.H./20 hours, 85℃/85%R.H./20 hours, the purpose of 85℃/85%R.H./20 hours is to let the module surrounding full of water, 20 hours dwell time is too short, is not enough for water to penetrate into the module and junction box inside.
Through wet freezing test: Module defects can be found: cracks, warping, severe corrosion, lamination of sealing materials, failure of adhesive delamination junction box & water accumulation, wet insulation **... Etc.
Test conditions: 85 ℃ / 85% R.H. (h) 20-40 ℃ (0.5 ~ 4 h), maximum heat up 100, 120 ℃ / h, and maximum temperature of 200 ° C/h.
6. Purpose of wet freezing test:
The wet freezing test method is mainly to perform two kinds of damage to the solar module in a snowy environment.
(1). High temperature and humidity (85℃/85%R.H.) drop to -4℃ before 25℃, humidity should be controlled at 85%+5% RH. The purpose of this is to simulate the high humidity sudden change before the snow.
Before the snow, the environment will show a high humidity state, and when the temperature drops to 0℃, the water gas around the module and the junction box sealant will freeze. When the water gas freezes, its volume will expand to 1.1 times of the original, and the destruction method of ice expansion after the water gas penetrates the material gap through the water gas to achieve the purpose of this test. At present, the statistical results of wet freezing have the highest damage to junction box sealant, which will cause junction box degumming and water, and the failure ratio of module is estimated at 7%.
(2). The purpose of heating up from low temperature (-40℃) and humidity (50℃/85%R.H.) is to simulate the temperature rise in the module at sunrise in a snowy climate. Although the outdoor environment is still below 0℃, the solar module will generate electricity when there is light, and because the snow is still on the module, the heat spot effect will occur in the module. The temperature inside the module will also reach 50 ° C.
7. wet heat test (Damp heat) test IEC61215-10-13:
Description: To determine the ability of the module to resist long-term moisture penetration, according to the test results of BP Solar, its 1000 hours is not enough. The actual condition is found that the time to make the module have problems needs at least 1250 hours. According to the current requirements of the specification, the wet heat test process is not powered on, but the future trend is also to be powered on (positive and reverse bias), because it can accelerate the aging and failure of solar cells.
Test conditions: 85℃/85%R.H., time :1000 hours Defects can be found through the wet and thermal test: CELL delamination EVA(delamination, discoloration, bubble formation, atomization, Browning), connection line blackening, TCO corrosion, spot corrosion, Thin-film yellow discoloration, junction box degumming off
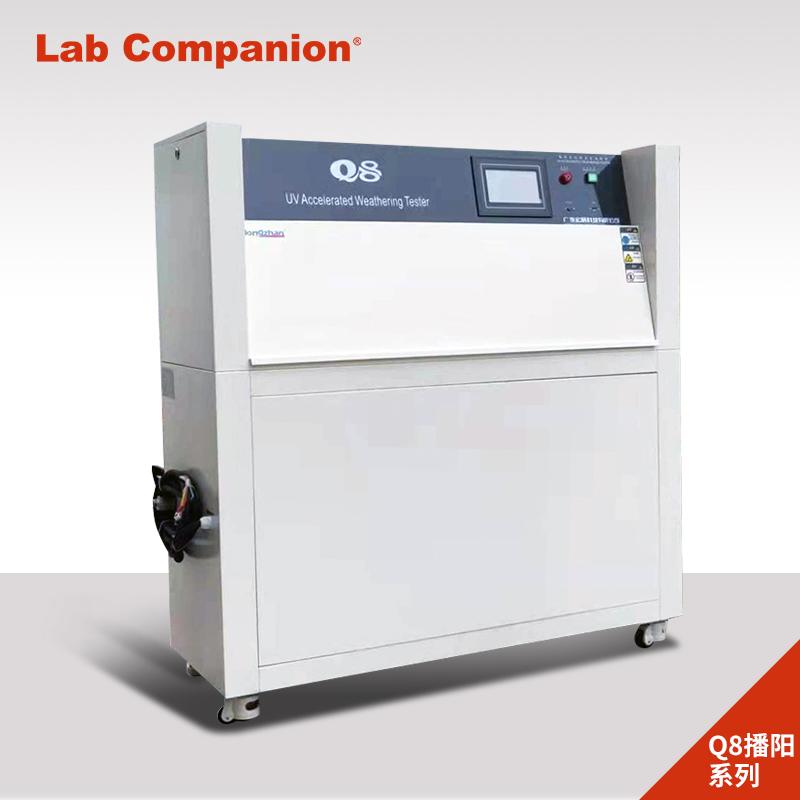